Manufacturing
How we make our world-leading products to help you change your game
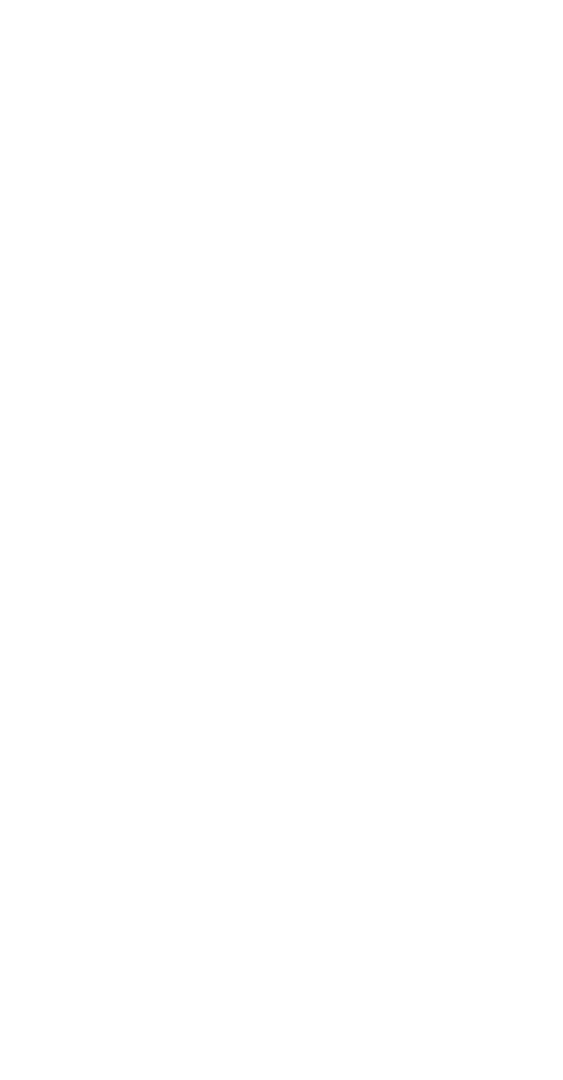
Our quality and safety processes are key to our success, with our skilled team managing a state-of-the-art manufacturing and testing facility to provide unbeatable reliability and support
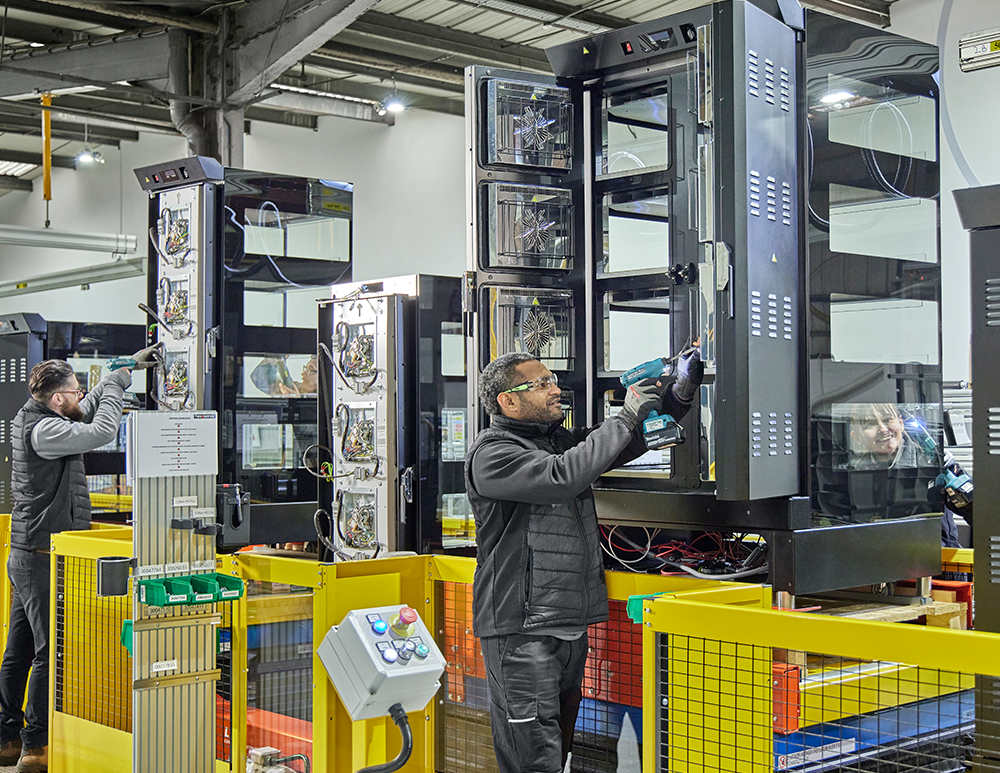
Investing in our processes
We have always committed to reinvesting in our products, processes and Partners, to make Flexeserve an ever-evolving brand. Most recently, we have invested over £300,000 in updates to our manufacturing facility – a key component within our overall operation.
These investments have been based on findings from our Product Innovation and Engineering team. Their work alongside experts from the automotive industry, who specialise in clean, simple manufacturing at the very highest quality, was pivotal in the decision-making process.
This has led to improvements within our production lines, adding semi-automation to give further support to our Manufacturing Partners that hand-assemble our units. We have also made significant changes in the layout of our facility to enhance productivity and ease pain points.
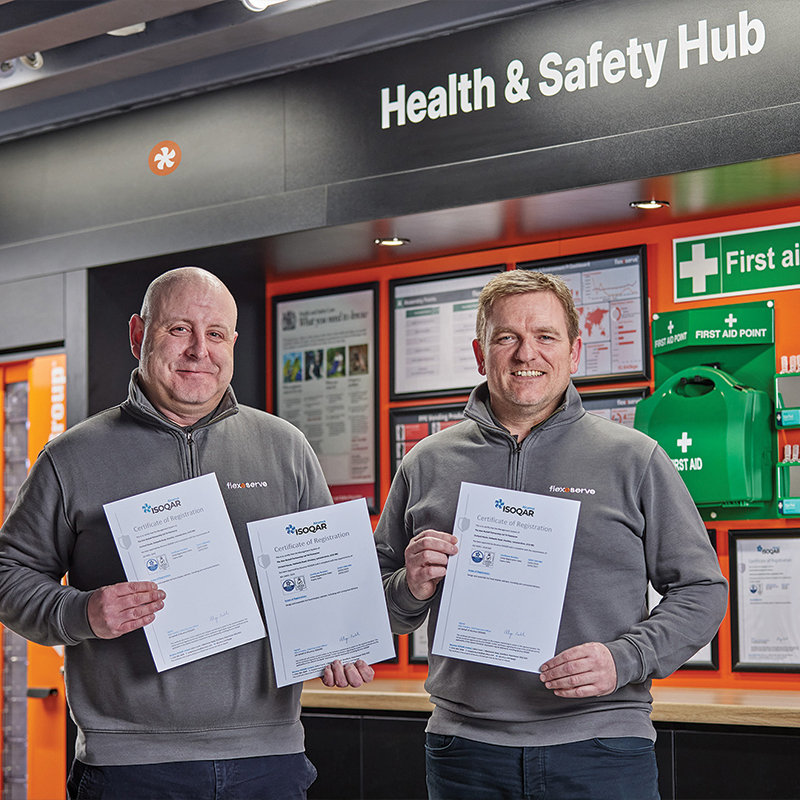
An ISO-certified business
Flexeserve has been awarded ISO 9001, ISO 14001 and ISO 45001 certifications, recognizing our commitment to quality, environmental, and health and safety excellence.
These international standards are pivotal in ensuring businesses operate responsibly, keeping their employees safe and helping everyone work to the best of their abilities.
In recognition of this significant milestone in our business, Global CEO Jamie Joyce, said: “This is an achievement that we’re all incredibly proud of – reflecting the high standards we’ve set and a testament to the hard work, dedication and spirit of collaboration that each of our Partners has demonstrated. Our collective efforts have been instrumental in achieving this goal.”
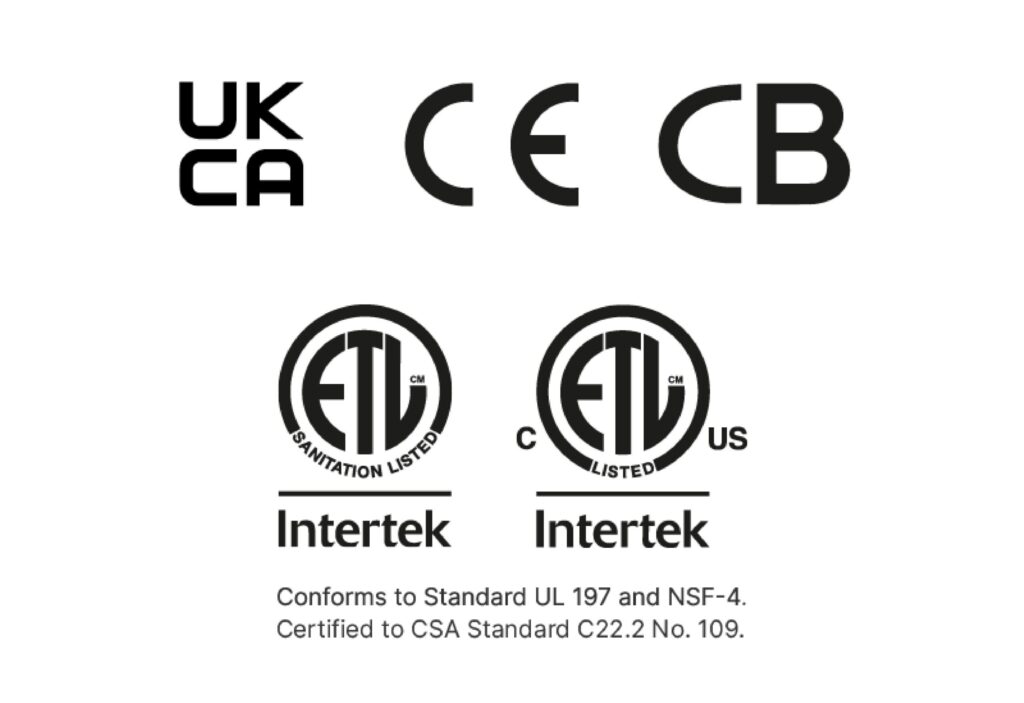
Accredited to the highest standards
Designed to be operated safely and with ease, all Flexeserve products are manufactured in compliance with the most stringent accreditations for export to Europe, USA, Canada and fifty CB Scheme member countries around the globe.
We are committed to upholding the strictest health and safety legislation and requirements, with approval from NSF, ETL Intertek standards and CE (Conformité Européenne) being fundamental in our process.
As part of this, our manufacturing facility is regularly audited to retain these certifications and ensure a high standard is met throughout.
We are passionate about how we manufacture the industry's leading hot-holding units.
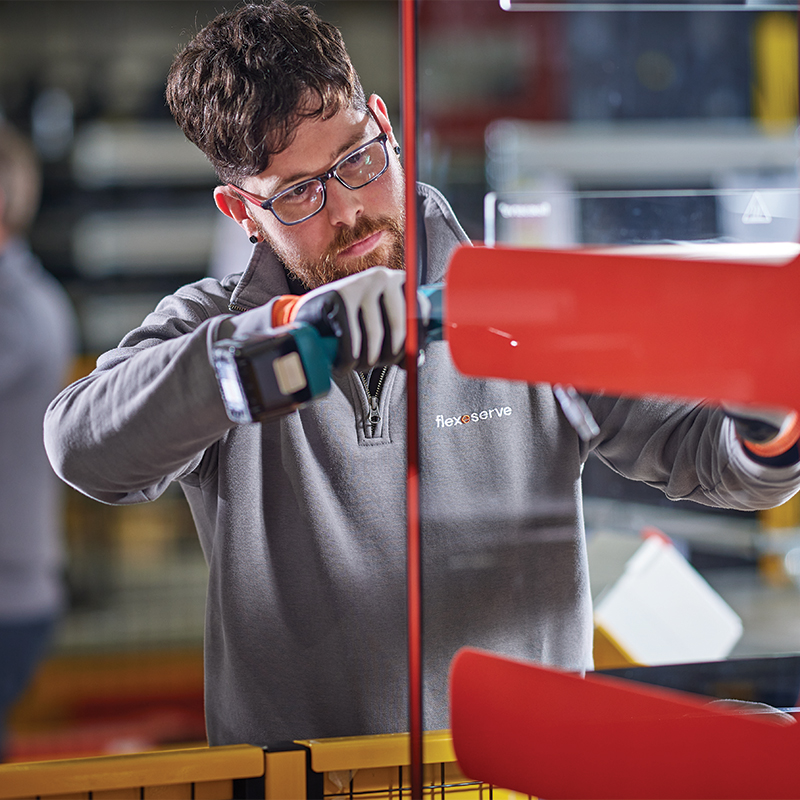
Prioritising HSEQ
Our Health, Safety, Environmental and Quality Department has set the standard for what is expected across the industry. We manufacture in a way that evokes the highest quality, whilst ensuring the wellbeing of our Partners and the planet.
All Flexeserve products are hand-assembled by our highly skilled team of Manufacturing Partners at our Global HQ in the UK. We are a proud British manufacturer that recognises the reputation of quality and reliability associated with this.
We have received the most prestigious award for UK businesses, a Queen’s Award for Innovation, for our world-leading technology. The quality associated with our unique hot-holding capabilities was significant in its success and was recognised in this achievement.
This need for quality is also reflected in our global supply chain. Our suppliers are industry-leading in their own right and together we ensure every product meets our high standards, selecting every component used in with excellence in mind.
Made responsibly
We are committed to Net Zero Carbon by 2030 as we look to increase on our wide scope of sustainability measures.
Across all our manufacturing operations and wider business, we have now eliminated reliance on gas and have significantly reduced electricity usage. This is only possible with improvements that scale to the smallest detail – for example, the application of motion-sensitive, LED lighting.
We continue to work closely with our supply chain partners to ensure the ethical and responsible sourcing of all the components found within our products. This has also extended to limiting our use of plastics within our shipping and packaging materials once we have completed your product.
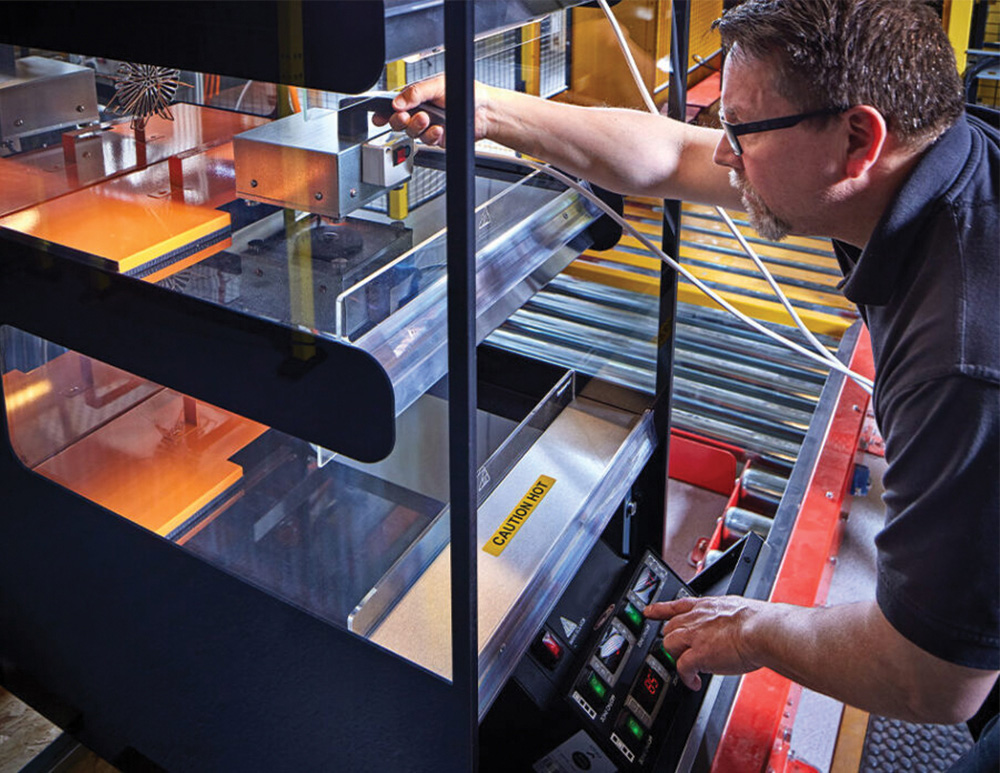
Testing you can rely on
Our products are designed in-house and capable of being customized through our highly detailed manufacturing process. This process also includes in-line testing, implemented from start to finish on every unit.
We test 100% of our products, rather than a small sample, to ensure complete transparency and reliability. This innovative testing process was designed in-house specifically for our own units, providing extreme accuracy in its outcomes and a high level of energy efficiency.
This results in a range of reliable and resilient products that cement us as the leaders in the industry.
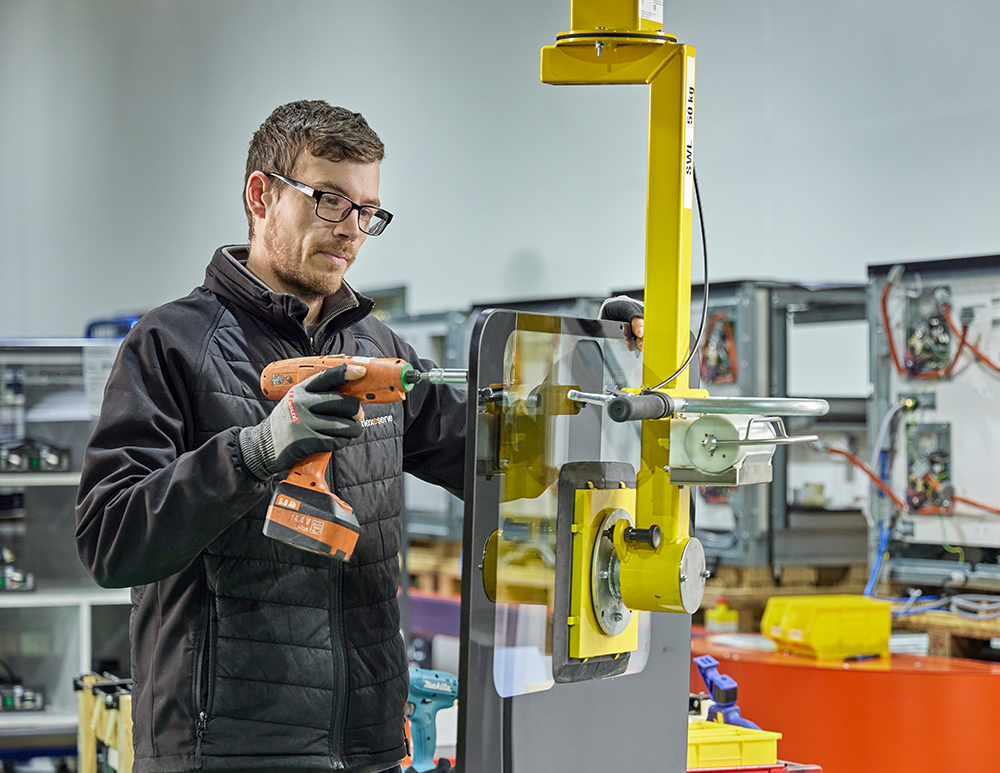
Manufacturing on a global scale
By focusing on each of these manufacturing elements, we can deliver on the growing demand for Flexeserve products and services.
We continue to attract major brands that operate on a global scale. With that, comes a requirement to supply our high-quality products in tighter timeframes and at higher volumes.
Thanks to our laser-focused approach to hot-holding, we’re able to dedicate 100% of our resources to ensuring our processes can be refined and optimized to meet the level of these brands’ operations. Our approach to Lean manufacturing enables us to use our time as efficiently as possible, creating a flow of production that can be maintained at any volume.